Powder coating
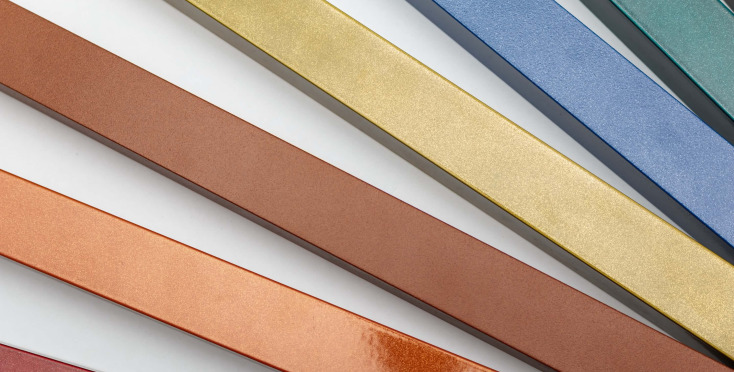
What is powder coating
Aluminum powder coating is a process used to apply a protective and decorative finish to aluminum surfaces. It involves the application of a dry powder. The powder is electrostatically charged and sprayed onto the surface of the aluminum, which has been pre-treated to ensure proper adhesion.
Once the powder is applied, the aluminum part is heated in an oven (curing process), causing the powder to melt and flow into a uniform coating, creating a durable and resistant finish. The result is smooth, even coating that provides protection against corrosion, abrasion, and other environmental factors.
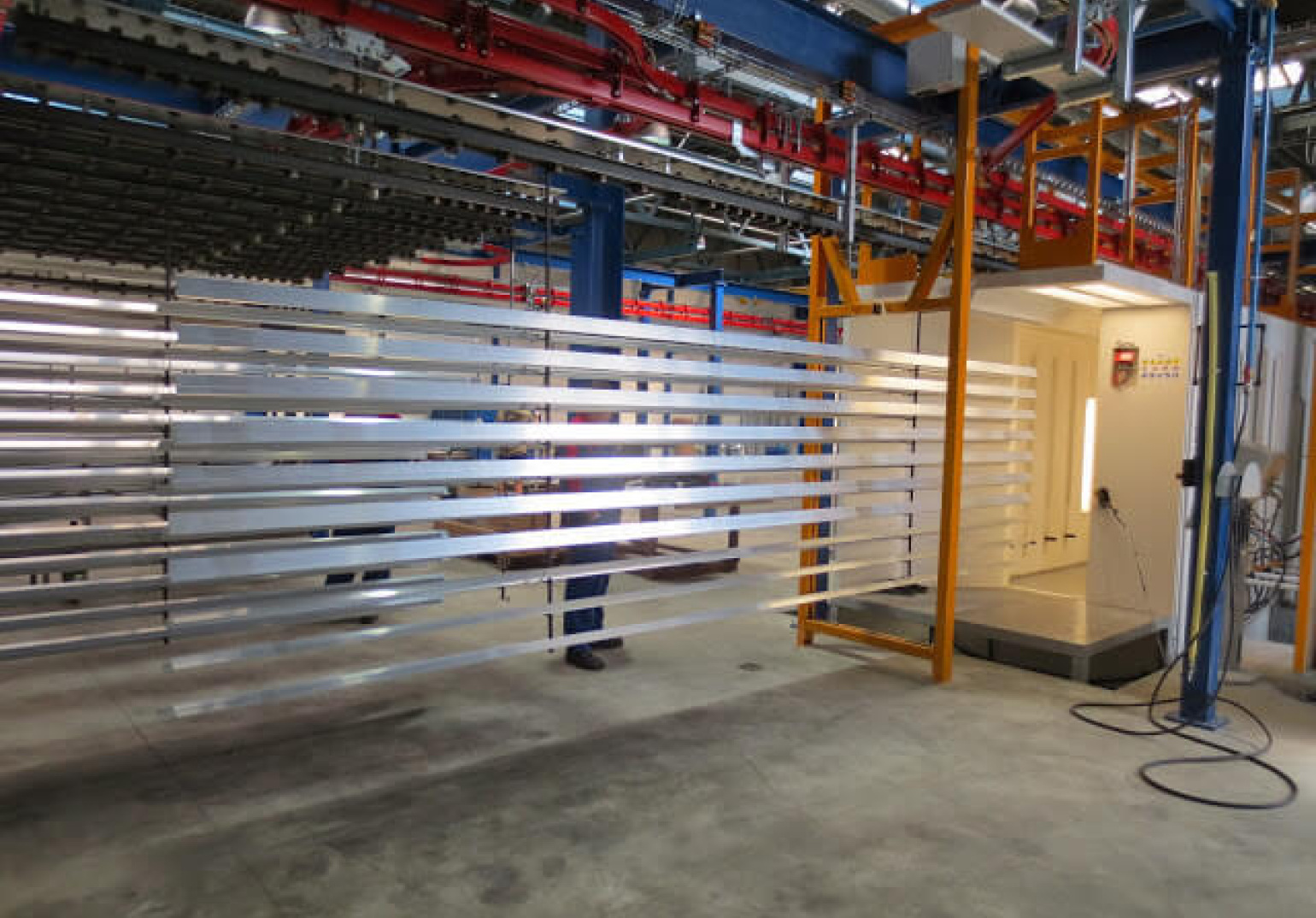
Powder coating advantages
Powder coating offers several advantages, including:
- Durability. Powder coatings are highly resistant to chipping, cracking and peeling, making them ideal for outdoor applications or harsh environments.
- Environmentally friendly: Powder coatings contain no volatile organic compounds, deducing harmful emissions and environmental impact compared to liquid coatings.
- Versatility: powder coatings come in a wide range of colors, textures and finishes, allowing for customization and creativity in design.
- Efficiency: Powder coating processes can be highly automated, resulting in higher production speed and lower labor costs.
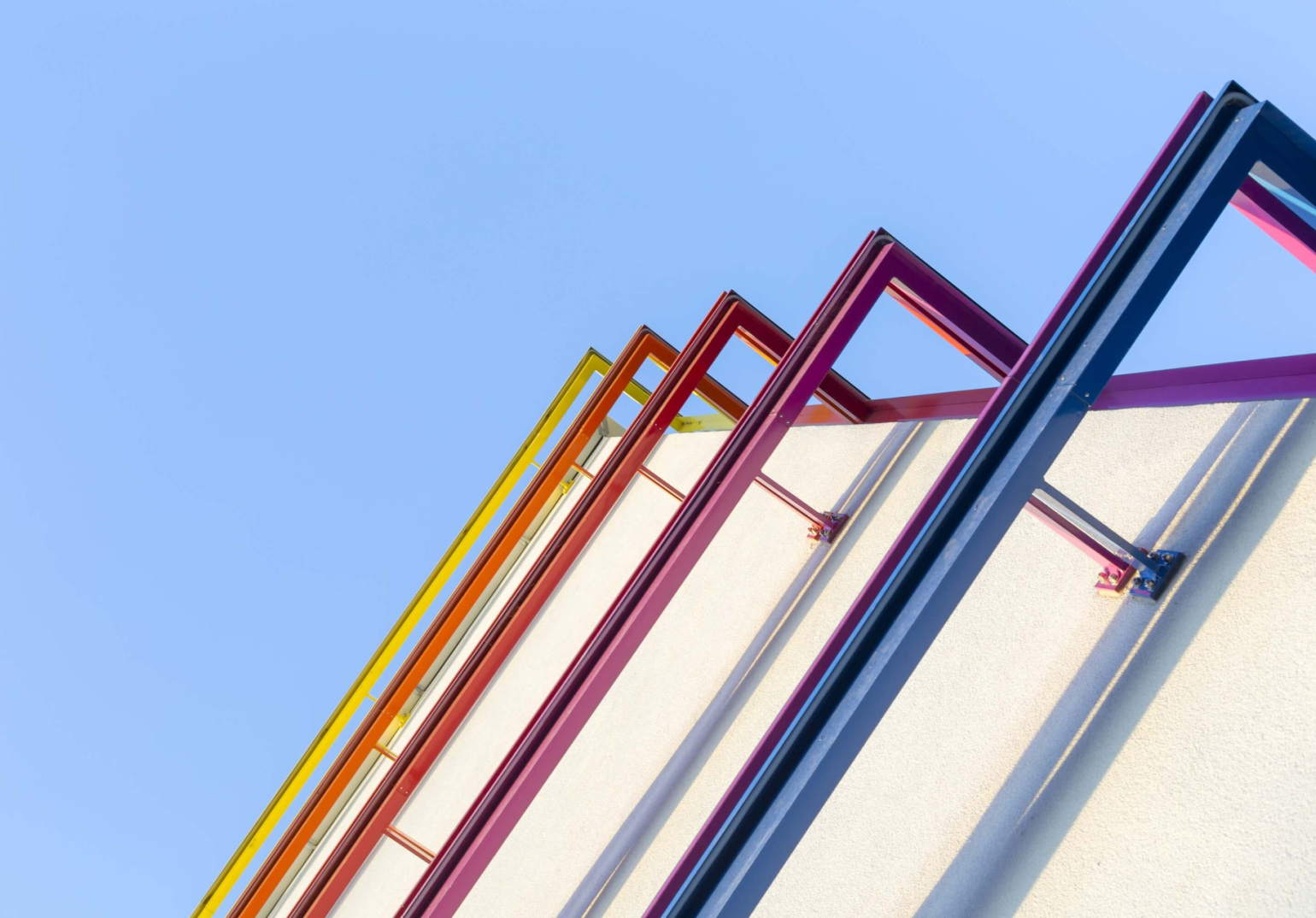
Choose right powder
Choosing the right powder for aluminum coating involves considering several factors such as the desired finish, application method, environmental conditions and performance requirements.
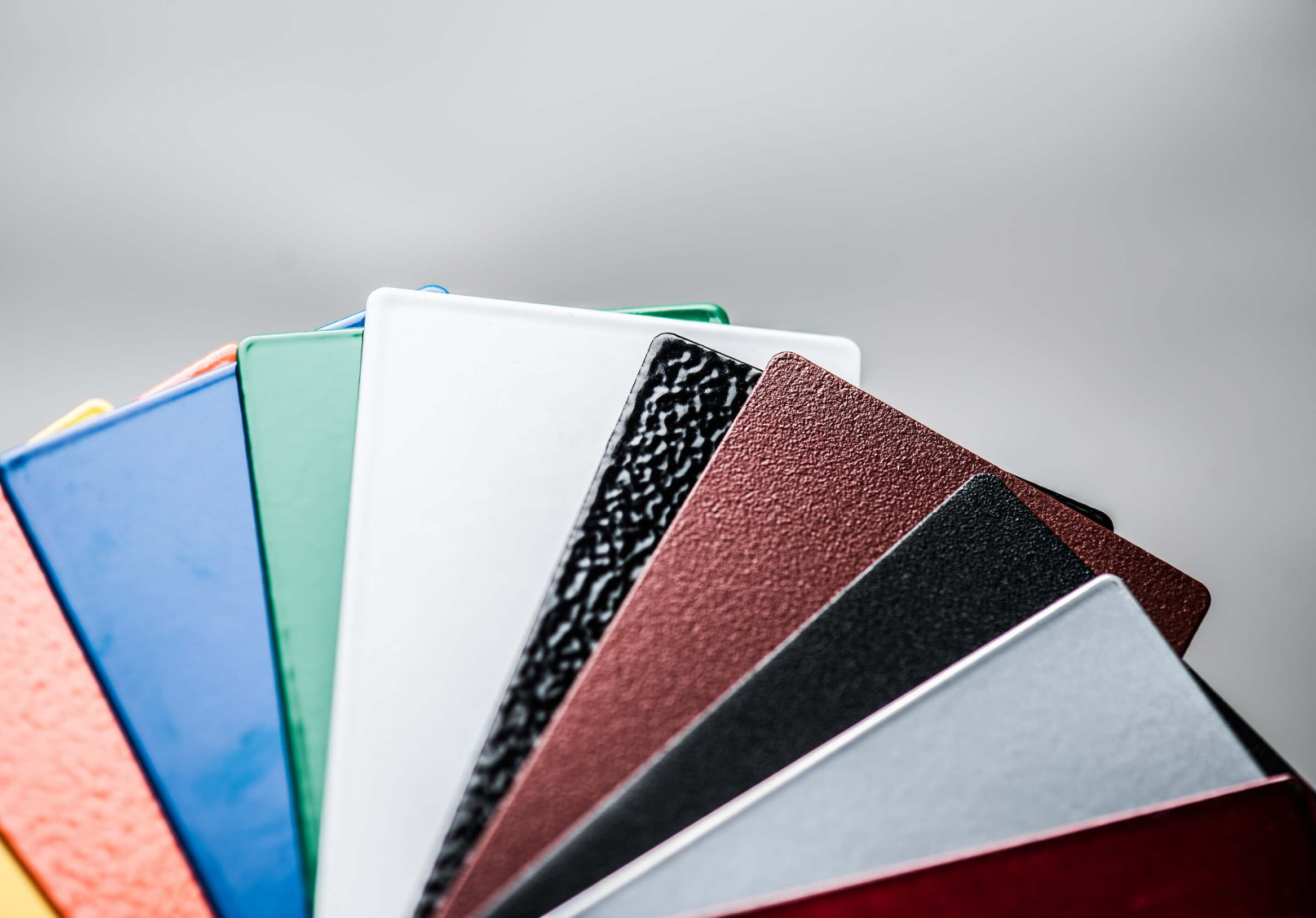
Here are some steps to help you select the appropriate powder coating for aluminum:
- Determine the application requirements: Consider the intended use of the coated aluminum parts. Are they for indoor or outdoor use? Will they be exposed to harsh chemicals, UV radiation or extreme temperatures? Understanding the environmental conditions and performance expectations will help guide your selection.
- Select the desired color and finish: Powder coatings come in a wide range of colors, textures and finishes, including glossy, matte, metallic and fluorescent.
- Consult with INLOOK: Work closely with a reputable powder coating supplier who can provide technical expertise and guidance in selecting right powder for your aluminum coating application. They can offer products recommendations, provide test samples and assist with troubleshooting any issues that may arise during the coating process.
- Coating material. Our high quality automated lines are dedicated for aluminum, but we can also accept galvanized or stainless steel products (with some exceptions)
- Sizes of work pieces. We can provide service for 1,4 m high, 0,4 m wide (0.5 m in EE) and 7,2 m (7.0 m in EE) long products
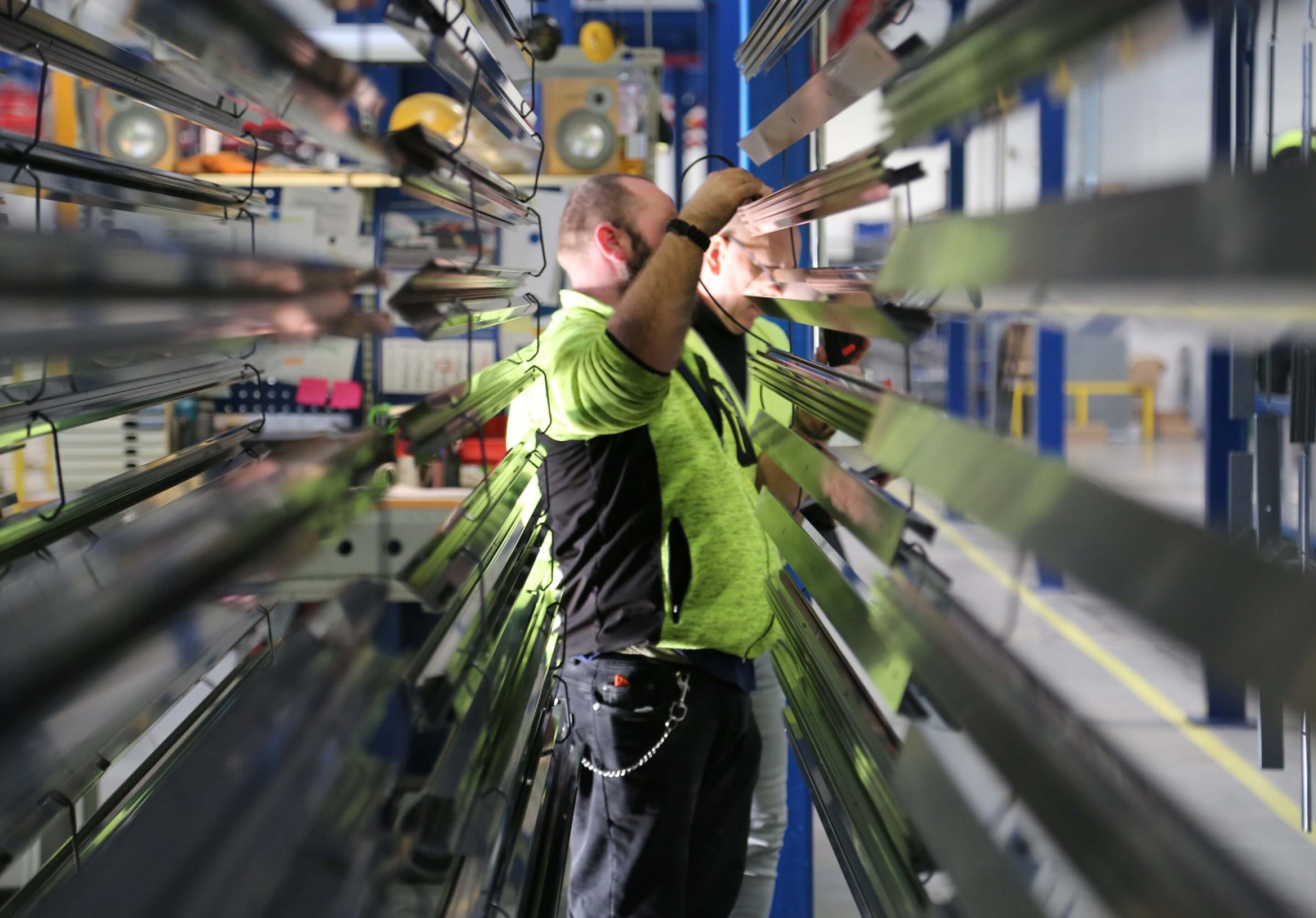
Things to note
- Surface preparation: Proper surface preparation is crucial for good adhesion and high-quality finish. Ensure that the aluminum surface is clean, dry and free of contaminants such as oil, grease, dirt and oxide layers.
- Pre-treatment: Depending on the specific requirements and conditions of the aluminum substrate, pre-treatment processes such as acid etching, conversion coating or sandblasting may be necessary to enhance adhesion and corrosion resistance.
- Powder application: The powder coating should be applied evenly and with the appropriate thickness to achieve the desired finish and performance.
- Curing temperature and time: Proper curing of the powder coating is essential for achieving optimal adhesion, hardness and durability. Typically, powders is cured at temperatures ranging from 150 °C to 200°C
- Cooling and handling: After curing coated aluminum parts need to be cooled down gradually before handling and further processing. Coated parts need to be handled with care to avoid scratching, chipping or other damages to the finish.
- Quality control: Implemented quality control measures to ensure consistency and reliability in the powder coating process. Performing visual inspections, adhesion tests, thickness measureme
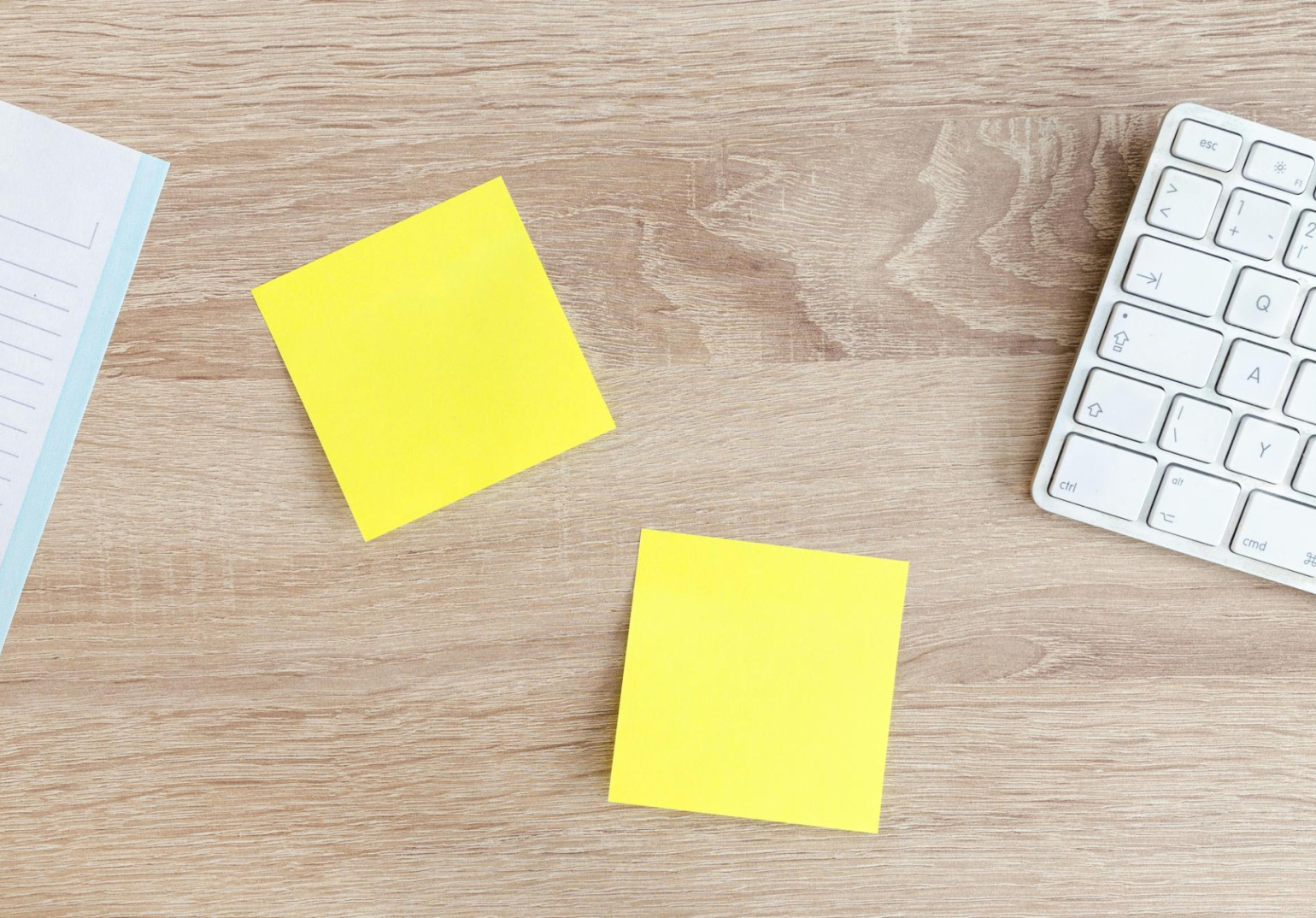